筆者公司有c2.2 m x 12 m回轉(zhuǎn)烘干機(jī)兩臺(tái),主要用于烘干粘土、礦渣、沸騰爐渣、鐵粉等原材料。在烘干初水份為15%~20%的礦渣時(shí),產(chǎn)量?jī)H有9~10.5 t/h,水份5%,煤耗高達(dá)38 kg標(biāo)煤/干料。該系統(tǒng)主要存在著燃燒爐膛溫度低、燃燒效率低、熱損失大、熱交換效率差、系統(tǒng)漏風(fēng)嚴(yán)重、電耗高,出機(jī)水份難以控制、原有袋收塵結(jié)露嚴(yán)重、經(jīng)常糊袋不能正常工作,通風(fēng)條件差,粉塵污染大等問題。如何實(shí)施烘干系統(tǒng)節(jié)能改造,提高現(xiàn)有烘干設(shè)備的生產(chǎn)能力和烘干質(zhì)量,降低電耗和生產(chǎn)成本,是迫切需要解決的問題。
針對(duì)烘干系統(tǒng)存在的問題,公司采取的主要技術(shù)改造措施如下:(1)對(duì)熱風(fēng)爐進(jìn)行改造;用自動(dòng)加煤的KBF22高溫沸騰爐取代手燒爐;(2)烘干機(jī)內(nèi)部揚(yáng)料板由單一式改為組合式;(3)通過加大風(fēng)機(jī)葉輪直徑,增加排風(fēng)能力,使廢氣及時(shí)排出;(4)把原袋收塵更換成KBD高效抗結(jié)露電收塵;(5)堵絕漏風(fēng)、加強(qiáng)系統(tǒng)保溫。通過一系列改造后,烘干礦渣產(chǎn)量由9~10.5 t/h提高到24。26 t/h,終水份由5%下降到1%,煤耗由38 kg降到13~14 kg,電耗降低60%,粉塵排放濃度<60.mg/m3(標(biāo)準(zhǔn)狀況),燃燒效率95%以上。改造后工藝流程如圖1示:
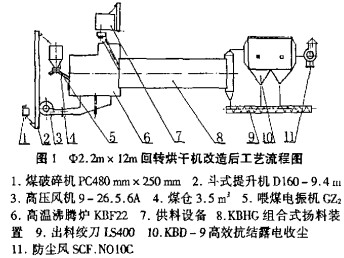
1、改人工加煤手燒爐(如圖2所示)為KBF22高濕沸騰爐
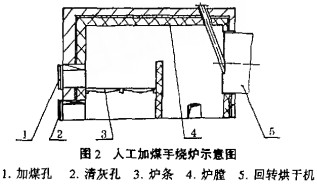
1.1 KBF22高溫沸騰爐主要優(yōu)點(diǎn)
(1)適應(yīng)性強(qiáng),可燃用各種劣質(zhì)燃料,如煤矸石、石煤、劣質(zhì)煙煤、無煙煤,煙道灰、造氣爐渣等。
(2)燃燒效率高,溫度均勻。燃燒效率高達(dá)95%以上,溫度在800~1050℃任意調(diào)節(jié),供熱平穩(wěn),促證了原料烘干產(chǎn)量、質(zhì)量的提高。
(3)污染物排量很小。燃燒充分,氯化物、硫化物排量達(dá)到國(guó)家標(biāo)準(zhǔn)要求。
(4)灰渣可搞綜合利用。沸騰爐的灰渣未經(jīng)高溫熔化過程,活性好,含硫及含碳低,可用來做水泥混合材或爐灰,也可用來提煉氧化硅等。
(5)勞動(dòng)強(qiáng)度小,操作環(huán)境好,有利于實(shí)現(xiàn)自動(dòng)化及安全文明生產(chǎn)。
1.2 KBF22高溫沸騰爐的改造過程
(1)拆除原有手燒爐膛內(nèi)外墻體及爐條:
(2)挖爐床風(fēng)室地坑及澆風(fēng)機(jī)混凝土基礎(chǔ);
(3)安裝爐床及等壓箱體,砌筑爐腔內(nèi)垂直段、護(hù)散段、懸浮段,同時(shí)把爐門、清灰門及加煤管砌人墻內(nèi);
(4)裝好大、小風(fēng)帽后,用牛皮紙包住通風(fēng)孔,澆注耐火澆注料;
(5)安裝高壓風(fēng)機(jī)及調(diào)節(jié)風(fēng)門;
(6)做好喂煤鋼架、煤斗及煤提升機(jī);
(7)安裝煤破碎機(jī)。
烘干加熱爐改造后如圖3示。
1.3 KBF22高溫沸騰爐操作注意事項(xiàng)
(1)沸騰爐砌好后,清除爐床上雜物,啟動(dòng)引風(fēng)機(jī)進(jìn)行空載試驗(yàn),一切正常后可關(guān)閉;
(2)爐內(nèi)鋪上黃砂(粒徑0.5,3 mm) 150~200mm進(jìn)行冷態(tài)試驗(yàn),目測(cè)砂子沸騰情況應(yīng)層次分明,平整無流溝;
(3)用木材烘爐,約24 h后略撇幾鏟煤,啟動(dòng)引風(fēng)機(jī)緩慢烘烤,約48 h后關(guān)掉引風(fēng),啟動(dòng)鼓風(fēng)機(jī)微量風(fēng)經(jīng)36—37 h,直到爐內(nèi)停冒汽為止;
(4)點(diǎn)爐時(shí),逐步加大風(fēng)量1%~2%,等爐內(nèi)出現(xiàn)一層藍(lán)色火焰時(shí),應(yīng)逐步增風(fēng),等碳煤層呈暗紅色火浪后,再不斷加煤,火焰呈桔黃色時(shí),應(yīng)緩慢加大鼓風(fēng)機(jī)的風(fēng)量,使整個(gè)爐面成沸騰狀態(tài),沸騰高度100~200 mm,在此狀態(tài)下,鼓風(fēng)機(jī)的風(fēng)量不再增加;啟動(dòng)喂煤系統(tǒng),使?fàn)t內(nèi)溫度緩慢上升到800~1 000;
(5)正常運(yùn)行時(shí),鼓風(fēng)機(jī)風(fēng)壓3 900 Pa,爐床溫度900℃左右,引風(fēng)機(jī)壓力- 10 Pa;
(6)根據(jù)負(fù)荷的變化及時(shí)調(diào)整喂煤量和送風(fēng)量,保證沸騰安全、經(jīng)濟(jì)、穩(wěn)定的運(yùn)行,注意調(diào)整爐溫時(shí),增減煤量的幅度不宜過大;
(7)如爐內(nèi)火色發(fā)黃、發(fā)白或溫度超過上限時(shí),應(yīng)停止供煤并向爐內(nèi)加砂壓火,以免爐內(nèi)結(jié)焦:如火色變暗,應(yīng)減少鼓風(fēng)量,再加一兩鏟煤;如突然斷煤時(shí),為防止死火,應(yīng)立即停止鼓風(fēng);
(8)鼓風(fēng)機(jī)風(fēng)壓升到標(biāo)定值后,就應(yīng)開始排渣,堅(jiān)持少排、勤排的原則,以防止?fàn)t溫波動(dòng),一般每次排渣風(fēng)壓降約100~500 Pa為好。
2、烘干機(jī)內(nèi)部揚(yáng)料板改造
原老式烘干機(jī)內(nèi)部揚(yáng)料板形式單一、布置不合理、數(shù)量較小,所以易形成“風(fēng)洞”難以形成均勻的料幕。在回轉(zhuǎn)烘干機(jī)系統(tǒng)中,物料與熱氣流直接接觸進(jìn)行熱交換,加大物料熱煙氣接觸面積,就能夠提高熱交換效率,而增加接觸面積的主要手段是在烘干系統(tǒng)內(nèi)部采用新型組合式揚(yáng)料裝置。該裝置使物料沿軸向呈“波浪式”向前“蠕動(dòng)”,不但提高了物料的拋撒均勻性,增加了物科的熱換交時(shí)間、翻轉(zhuǎn)次料和烘干次數(shù),而且該裝置每一組揚(yáng)料板在徑向位置上都有多種角度的組合,通過角度的變化補(bǔ)償因時(shí)間差產(chǎn)生的撤料間隙性,避免了“風(fēng)洞”、“階梯撒料”,從而提高了烘干熱效率及烘干產(chǎn)量。
3、收塵系統(tǒng)改造
3.1 加強(qiáng)系統(tǒng)通風(fēng),杜絕漏風(fēng)
(1)增加風(fēng)機(jī)葉輪直徑,加大通風(fēng)能力,使廢氣及時(shí)排出。
(2)喂料、出料及降塵端加強(qiáng)鎖風(fēng)、漏風(fēng)措施。
(3)烘干窯頭、窯尾采用石墨塊密封,防止冷風(fēng)進(jìn)入。
3.2 改玻纖袋收塵為高效抗結(jié)露電收塵
(1)不怕結(jié)露、永不結(jié)穿;恒流源加上高壓進(jìn)線與高壓絕緣系統(tǒng)底與煙氣分離。
(2)雙層保溫結(jié)構(gòu)及恒溫控制儀,即使在20~50℃情況下也毫無負(fù)面影響。
(3)采用方形結(jié)構(gòu),除塵面積比其它類結(jié)構(gòu)大20%,完全解決了二次揚(yáng)塵,除塵效率≥99.9%。
(4)功率因素高達(dá)0.96,節(jié)能效果顯著。
(5)占地面積小,無需土建,易安裝,投資少。
4、烘干系統(tǒng)改造后技術(shù)效果及技術(shù)經(jīng)濟(jì)分析
(1)烘干系統(tǒng)增產(chǎn)幅度大,節(jié)能效果顯著:烘干硫渣產(chǎn)量提高了166%,由9~ 10.5 t/h提高到24~26t/h,終水份由5%下降到1%,煤耗降低65.8%,由38Kg降到13~14 kg,電耗降低60%。
(2)采用新型高溫沸騰爐,升溫快,保溫性能好,燜火時(shí)間長(zhǎng),不需要經(jīng)常點(diǎn)火,減輕了工人勞動(dòng)強(qiáng)度,燃燒效率95%以上,爐渣可作混合材用。
(3)烘干系統(tǒng)熱率高,蒸發(fā)強(qiáng)度大,利用新型組合式揚(yáng)料裝置,重新排列組合后,使物料停留時(shí)間,延長(zhǎng)了50%,強(qiáng)化了烘干效果。
(4)用劣質(zhì)煤取代優(yōu)質(zhì)煤,每噸煤成本下降150元,每年僅節(jié)煤一項(xiàng),節(jié)約40多萬元,效益顯著,6~8個(gè)月即可收回投資。
(5)高效抗結(jié)露電收塵效果好,排放濃度<60mg/m2(標(biāo)準(zhǔn)狀況),完全達(dá)到國(guó)家排放標(biāo)準(zhǔn)要求。
三門峽富通新能源銷售烘干機(jī)、干燥機(jī)、顆粒機(jī)、秸稈壓塊機(jī)等機(jī)械設(shè)備。