某公司有一臺Ø1.5 x12.0m轉(zhuǎn)筒烘干機,原采用噴煤粉燃燒室順流式烘干工藝,燃用優(yōu)質(zhì)煙煤,筒內(nèi)安裝普通弧形結構揚料板,存在烘干效果差、產(chǎn)量低、成本高等缺點。為此我們對其進行了系統(tǒng)的技術改造。
1、改造內(nèi)容
1.1 燃燒室的改造
原噴煤粉燃燒室因其結構不合理,煙煤燃燒溫度高,系統(tǒng)漏風量大,烘干機人口煙氣溫度高,且時有煤粉噴至入口處明火燃燒等諸多缺點,導致系統(tǒng)熱效率低,故障率高,經(jīng)常燒塌爐膛,燒壞喂料管和進料螺旋簡;維修量大成本高,維修周期短(僅3個月)。經(jīng)分析研究,決定拆除原燃燒室,改建了高溫煙氣沸騰爐燃燒室。其構造如圖1所示。
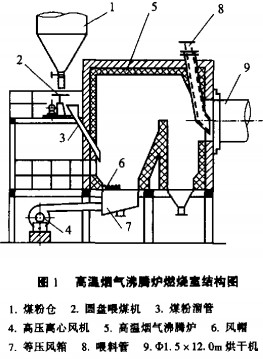
它由送風系統(tǒng)、煤粉制備燃燒系統(tǒng):儀表檢測控制系統(tǒng)和爐體部分組成。送風系統(tǒng)主要設備是一臺高壓離心風機,它通過等壓風箱和風帽向爐內(nèi)鼓入一定壓力和流量的風,以供充分燃燒所需的足夠氧氣,并保證沸騰床達到良好的沸騰狀態(tài)。燃燒所用的煤粉存于煤粉倉中,由圓盤喂料機根據(jù)爐膛溫度,通過熱電偶反饋,自動跟蹤和調(diào)節(jié)給煤量。圓盤喂料機在額定范圍內(nèi)采用調(diào)速電機無級變速。儀表檢測控制系統(tǒng)采用熱工儀表對爐膛各部分的溫度、壓力進行檢示、控制。它能實現(xiàn)聯(lián)鎖控制和自動報警。
1.2 筒內(nèi)結構的改造
烘干機筒內(nèi)原裝普通弧形揚料板揚料,效果差(其工作狀況如圖2)。
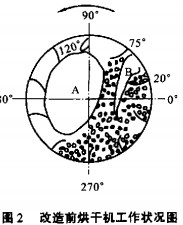
因其結構不合理,物料只能在第1象限內(nèi)拋撒,這就導致了烘干機橫斷面上易出現(xiàn)“風洞”及“階梯式”料柱(圖中A、B區(qū)域),物料分散度差,傳熱效率低,出機物料水分難以控制等。改造后的組合式揚料板是根據(jù)物料的烘干原理,結合生產(chǎn)實際而優(yōu)化設計的一種較為理想的揚料裝置。如圖3、圖4所示。
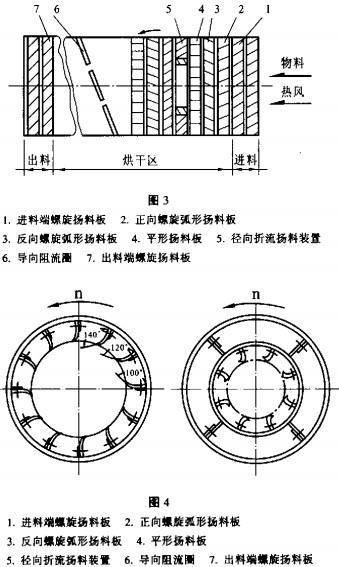
進料端采用正向螺旋揚料板,便于預熱后的物料順利進入烘干階段。該揚料裝置保證進入烘干機的物料在其橫斷面上呈“瀑布”狀下落。整套揚料裝置具有一定的導向、均流及阻料等多種性能,增加了物料與熱氣流的接觸面積和料流阻力,延長了物料在機內(nèi)停留時間,從而提高了烘干機熱效率,并為適當提高筒體轉(zhuǎn)速創(chuàng)造了條件。由于每組揚料板在徑向布置上又呈多角度變化,也大幅度提高了烘干效率。
2、改造效果
本次技改利用春節(jié)前后水泥市場淡季和生產(chǎn)線年度大檢修的契機實施,沒有影響正常的生產(chǎn)經(jīng)營。該項目自2001年1月13日開始拆除舊爐膛,到2月10日工程改造結束,進入調(diào)試階段,2月15日正式投料生產(chǎn),工期僅一個月時間。總投資17,2萬元。
(1)高溫煙氣沸騰爐的采用,對燃料的適應性增強,能燃燒2000×4.186kj/kg以上的各種劣質(zhì)煤;熱效率達85%以上,燃料的燃燼率高于95%,灰渣的含碳量低于5%,且是活性很好的水泥混合材;節(jié)能效果顯著,比改前煤耗下降了25%以上;儀表自動檢測控制,機械化、自動化程度高,減輕了工人的勞動強度;密封性能好,環(huán)境得到凈化;點火升溫快,調(diào)節(jié)靈活,可壓火備用48小時以上。
(2)改造后的新型組合揚料裝置的使用,使物料在烘干機內(nèi)停留時間增加了25, 9%,物料填充系數(shù)增加了66.3%,烘干機的熱效率提高了66%,煤耗下降20%以上,筒體可在0~5s/min的范圍內(nèi)實現(xiàn)
調(diào)速運行。
改造前后主要熱工、工藝參數(shù)對比如表1(實測)。
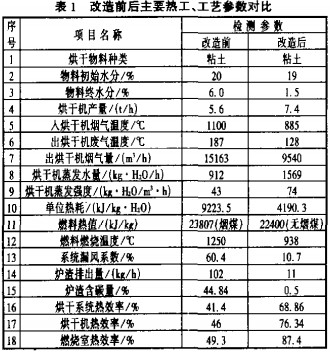
3、結束語
此次技術改造是成功的:自投產(chǎn)以來,運行良好,挖掘了烘干系統(tǒng)的生產(chǎn)潛力。改善了系統(tǒng)工藝狀況,減輕了勞動強度,治理了環(huán)境污染。提高了系統(tǒng)的完好率和運轉(zhuǎn)率,延長了爐膛、喂料管、烘干機螺旋筒及其它相關輔機設備的壽命。減少了維修量。節(jié)約了能源,尤其是無煙煤替代煙煤的燃燒也帶來了經(jīng)濟效益(兩者噸價格相差百多元)。
三門峽富通新能源生產(chǎn)銷售顆粒機、滾筒烘干機、烘干機、干燥機等機械設備。