生物質顆粒燃料的生產工藝,包括選料、粉碎、顆粒機制粒和打包四個步驟,同時該工藝中使用的生物質顆粒燃料顆粒機,包括兩個環模,兩個環模為外切圓柱體并相向旋轉,每個環模上均勻分布有若干壓制通孔,同一豎直截面上的壓制通孔均朝向所在截面的環模圓心,壓制通孔在兩個環模的相切處相間分布。顆粒機生產過程有效降低了能耗,整個生產制粒過程的單位能耗為25~60kWh/t,比傳統加工減少70%以上,同時在濕度為10~35%時可以一次成粒,省去了干燥工序,且成粒以后,只升溫10~15℃,壓制出來的顆粒溫度一般只有55~60℃,無需冷卻即可直接進行打包,又省去了冷卻工序,提高了工作效率,顆粒機壓制的顆粒燃料如下圖所示:
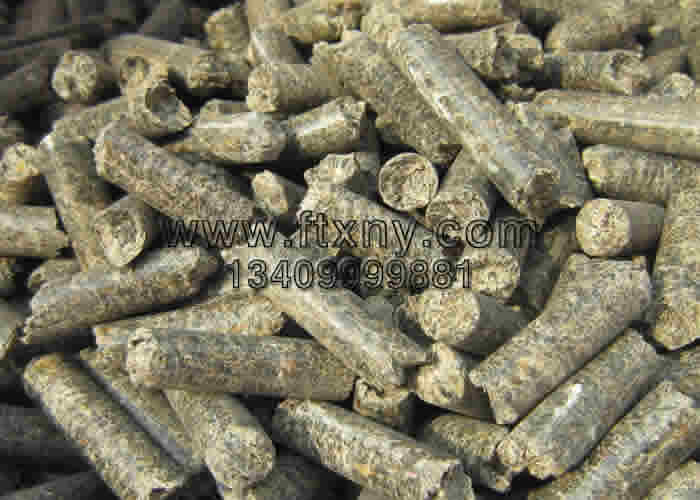
b.粉碎:將原料送入秸稈粉碎機內粉碎;
c.制粒:將粉碎后的原料送入生物質顆粒燃料顆粒機中,壓制成型;
d.打包:將壓制成型后的顆粒燃料直接送入打包機打包。
2、生物質顆粒燃料生產工藝,其特征在于:b步驟粉碎后原料粒度為4~5mm。
3、一種在所述要求1制取工藝中使用的生物質顆粒燃料顆粒機,其特征在于:包括兩個環模(1),所述兩個環模(1)為外切圓柱體并相向旋轉,每個所述環模(1)上均勻分布有若干壓制通孔(2)。
4、根據上述3所述的生物質顆粒燃料制粒機,其特征在于:同一豎直截面上的所述壓制通孔(2)均朝向所在截面的環模(1)圓心。
5、根據上述3所述的生物質顆粒燃料制粒機,其特征在于:所述壓制通孔(2)在兩個環模(1)的相切處相間分布。
煤、石油、天然氣等礦物燃料是工業社會的核心能源,但它們是不可再生資源,儲藏量有限。據國際能源機構統計,煤、石油、天然氣可供開采的年限分別只有240年、40年和50年。隨著人類經濟社會的飛速發展,能源消耗的速度越來越快,尤其是礦物燃料消費的不斷增加,導致了對它們的過度開采,使得價格日益上漲并漸趨枯竭;同時,高強度的利用使多余的能量和碳素大量釋放,打破了自然界的能量和碳平衡,造成臭氧層破壞、全球氣候變暖、酸雨等災難性后果,引起了國際社會的極大憂慮。如果沒有新的能源來取代常規能源在能源結構中的主導地位,21世紀必將發生嚴重的、災難性的能源和環境危機。
為此人們把視線聚焦到可再生能源身上。太陽能、風能、小水電等雖然是可再生能源,但不能進行物質生產,而生物質既能貢獻能量,又能像煤炭和石油那樣生產出千百種化工產品。如燃料乙醇與車用普通汽油相比,一氧化碳的排放可降低7%,碳氫化合物可減少48%;生物柴油富含氧,與普通柴油混合使用,可使燃燒更加充分,據檢測,生物柴油無毒,能進行生物降解,添加20%的生物柴油,可減少排放二氧化硫70%,降低空氣毒性90%;使用生物塑料能解決白色污染問題。同時生物質能源以作物秸稈、畜禽糞便、農林廢棄物、城市有機垃圾等為原料,使之無害化和資源化,將植物蓄存的光能與物質資源深度開發和循環利用,符合發展循環經濟的理念。因此,生物質能源既能滿足緩解能源危機的需要,又符合保護環境、實現可持續發展的要求,是中國進行可再生能源開發利用的必然選擇。
傳統的生物質顆粒燃料制取工藝為先選料,將原料干燥之后進行粉碎,粉碎后的原料送入顆粒機中壓制成型,對成型的顆粒燃料送入逆流式冷卻器進行冷卻,冷卻至允許溫度后送入打包機進行打包。在該工藝中使用的生物質顆粒燃料制粒機包括進料口、壓輥、主軸和壓模,原料從進料口進入落到壓模上,通過主軸的轉動帶動壓輥滾動,在壓輥的擠壓作用下,原料進入壓模的成型孔內壓縮成型,從成型孔另一端擠出。采用上述制取工藝和制取設備需要消耗大量電能、設備損耗大、生產成本高,通常單位能耗為80~180kWh/t,在濕度較大的情況下需要先對原料進行干燥才能進入制取設備成型,且在成型后顆粒升溫大,又需要進行冷卻才能進行打包,工作效率低下。
所要解決的技術問題在于提供一種生物質顆粒燃料制取工藝,可以有效解決傳統制取方法能耗大,生產成本高,在濕度較大的情況下需要先進行干燥而無法一次成粒,且成粒后需要先進行冷卻才能打包導致工作效率低的問題。
(轉載請注明:富通新能源顆粒機www.jiankongpf.cn)