整體式環(huán)模。整體式環(huán)模的主要結構參數有:環(huán)模直徑、環(huán)模厚度、環(huán)模有效寬度、模孔形狀、模孔直徑、模孔有效深度、模孔間壁厚以及環(huán)模的壓縮比、粗箍度等。
環(huán)模模孔的長度與模孔直徑的比值習慣上稱為環(huán)模的壓縮比它是反映燃料顆粒擠壓強度的一個重要指標。壓縮比越大,擠出的燃料密度越大,對于成型秸稈類生物質壓縮比一般為6~10左右。
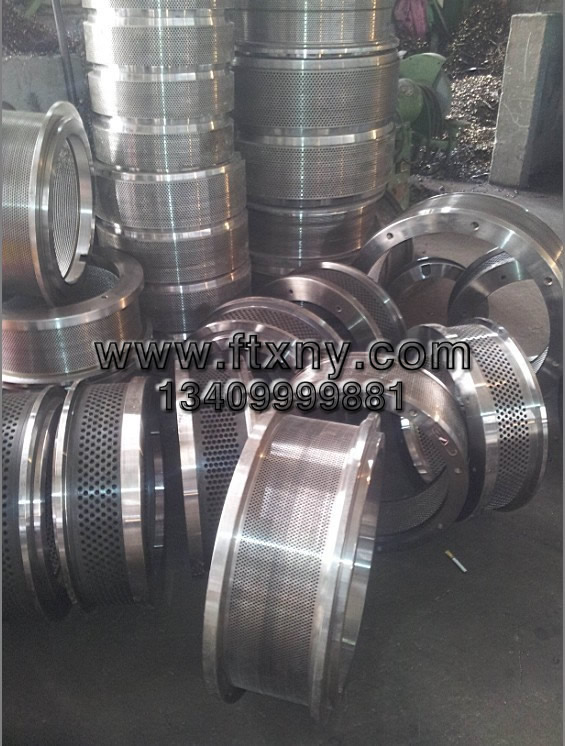
環(huán)模模孔開孔率越高,則出料越多,有利于提高生產率,但模孔間壁厚度變小,環(huán)模強度減小,容易開裂,所以要選擇合適的壁厚來保證環(huán)模的強度和開孔率。一般來說,模孔直徑越大,環(huán)模的開孔率越高;開孔率越高,出料越通暢,但環(huán)模強度也降低了。成型擠壓力大的原料,環(huán)模的開孔率適當小一些,保證環(huán)模的強度,防止環(huán)模開裂。
環(huán)模的厚度直接影響產品質量,環(huán)模的工作面積與設計功率成正比,功率一定對,環(huán)模應有對應的有效寬度,一般環(huán)模的有效寬度為10~14cm,分體模塊式環(huán)模大一些,顆粒環(huán)模小一些。環(huán)模厚度是一個關鍵參數,其影響因素很多,要根據不同原料種類經過認真工程試驗再定型。環(huán)模成型腔和壓輥是環(huán)模成型顆粒機的核心部件,其中的成型腔設計和加工又是關鍵技術,因此要對設備應用的范圍、對象等作詳細分析,不可一概而論,不可能有萬能成型顆粒機,要做多因素分析。
整體式環(huán)模磨損后需要整體更換,不僅增加維修成本,還會嚴重影響企業(yè)正常生產。因此環(huán)模材料的選用顯得尤為重要。目前,我國整體式顆粒環(huán)模成型顆粒機多數是沿用顆粒飼料成型顆粒機的設計,選用4Cr13不銹鋼和42CrM04合金結構鋼作為環(huán)模的材料。4Cr13不銹鋼的剛度和韌性都較好,采用整體淬火熱處理后,其硬度大于HRC50,并具有良好的耐磨性和耐腐蝕性,使用壽命較長。42CrM04合金結構鋼的機械強度高,淬透性高,韌性好,淬火時變形小,高溫時有較高的蠕變強度和持久強度。
用秸稈類原料生產顆粒成型顆粒燃料是不合算的,粉碎能耗高,磨損快。秸稈原料含有較高的堿性氧化物,成型孔磨損很快,在硬度小于HRC60的條件下,維修周期在300 h左右,可擴孔維修1或2次,但成型率降低。二次維修周期更短,因此秸稈顆粒是不適宜用整體環(huán)模技術的。
套筒式環(huán)模。套筒式環(huán)模由母環(huán)和套筒組成,套筒安裝在母環(huán)上。套筒的模孔可按成型理論單獨設計加工。模孔的結構應具有預壓成型段、成型段和保型段,各段尺寸應設計合理。套筒與環(huán)模可通過螺紋或嵌入的方式套裝。由于采用了套筒模孔,套筒模孔磨損后可實現(xiàn)快速更換,從降低設備加工成本和節(jié)約維修成本方面分析,套筒式環(huán)模優(yōu)于分體模塊式環(huán)模。
套筒式環(huán)模要注重三個方面技術的應用,一是母環(huán)的設計與加工,原則上母環(huán)的整體是不更換的,因此它的強度和成型套筒座的尺寸精度要保證,為降低成本可用鑄造技術生產。二是套筒的設計,內孔要有保證燃料質量的成型角和保型段長度,外部尺寸要滿足母環(huán)要求。材料可以是非金屬材料,也可以是耐磨鑄鐵材料。三是要更換方便,便于用戶操作。
套筒環(huán)(平)模在成型顆粒燃料發(fā)展中具有方向性,需要重點解決的是盤面的磨損維修與套筒更換的一致性。
分體模塊式環(huán)模。分體模塊是環(huán)模的核心部件。模塊入口部位的結構是生物質壓縮成型的關鍵技術之一,其結構尺寸、加工質量和精度直接影響環(huán)模的使用壽命,以及成型顆粒機生產能力和產品質量,對用戶的使用成本也有很大影響。根據生物質成型理論可將模塊組合后的成型腔分為三個階段:預壓階段、成型階段和保型階段。
成型腔中的生物質原料進入模輥間隙到壓縮終了稱為預壓階段,分體模塊模孔的人孔坡口,模輥間隙、料層厚度、壓輥轉速等參數影響預壓效果。模輥間隙大、料層厚、壓輥轉速高,預壓效果變差,磨損加快、耗能增加。從模孔坡口下端到保型段開始為成型階段,模孔這一部分的結構應設計成內錐形,成型角一般為10~30。這一段是保證原料產生塑性變形所需的擠壓力和成型密度的關鍵階段,原料對模孔的磨損最為嚴重,對模塊熱處理性能特別是耐磨性要求較高,成型角磨損變化后,成型率就會降低,分體模塊就要更換。實踐證明,更換是成批的,不可能是個別的;成型段過后,密實原料進入保型段,這一段的直徑略大于成型段出口尺寸,作用是消除在成型段產生的內應力,使成型顆粒燃料達到松弛密度的工藝要求,成為最后產品。
由上述分析可以看出,分體模塊的模孔具有成型和保型的功能,模孔的長度即分體模塊的厚度也應保證成型和保型功能的實現(xiàn)。成型和保型段的長度應根據不同種類原料的特性、模孔形狀、成型塊截面面積及要求的成型密度來確定。目前市場上的分體模塊式成型顆粒機大都將模塊厚度設計得比較小,保型段的長度不夠長,使得成型效果不好、成型質量不高。加工30~50 mm的棒(塊)狀成型顆粒燃料,分體模塊模孔的長度不得小于10cm,與燃料斷面尺寸的比一般為1:(6~8),可根據不同條件變化。
模塊失效的形式主要表現(xiàn)在兩個方面:一是模孔人口處產生的嚴重磨損和應力集中導致開裂而報廢,如圖6.7所示;二是保型段過度磨損而報廢。模塊的使用壽命不僅僅與選用的材料、加工工藝有關,還與生物質原料類型、燃料成型工藝參數、操作方法有密切關系,即使相同的模塊材料和相同的加工工藝,當上述條件不同時,模塊的使用壽命也相差很大,尤其縣檬孔人口處的磨損和開裂更為突出。
分體模塊的材料可根據成型的生物質原料種類、物理特性來選用。一般加工棒狀或塊狀成型顆粒燃料可選用35號或45號優(yōu)質碳素結構鋼,以及20Cr、40Cr、40CrMnMo等合金結構鋼,重要的是上述材料的熱處理工藝和磨損后的修補方法。
由于分體模塊式環(huán)模磨損后是群體換修,因此工作量和成本都比較高,其難度不比整體式維修小,對燃料生產單位來說,操作難度高,這是工程化階段出現(xiàn)的新問題。因此要進行技術集成再創(chuàng)新,目前本書參編單位采用的金屬噴涂工藝取得較好效果,但受條件限制也不能到設備使用單位進行維修。
(轉載請注明:富通新能源顆粒機www.jiankongpf.cn)